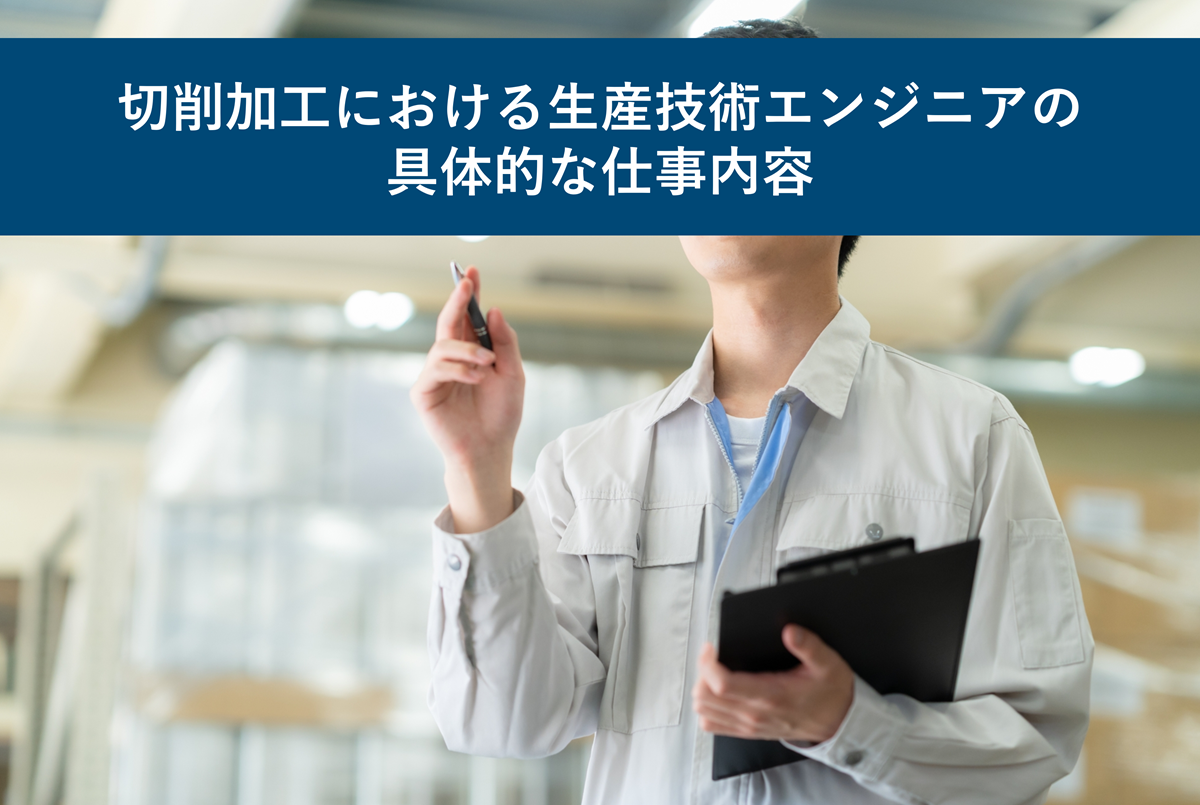
切削加工における生産技術エンジニアの具体的な仕事について詳しく知りたくありませんか。
この記事は生産技術アウトソーシングサービスを提供する辰星メタルパートナーに記事執筆を依頼し、切削工具と切削加工業界に特化した専門サイト「タクミセンパイ」が編集しました。
本記事では生産技術エンジニアの具体的な仕事内容として「工作機械の選定」「切削工具の選定」「加工条件の設定」などについて紹介しています。
この記事を読むことで、切削加工における生産技術エンジニアの具体的な仕事内容がわかるだけでなく、各業務のポイントを知ることができます。

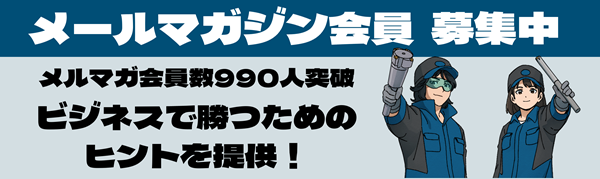
切削加工における生産技術エンジニアの具体的な仕事内容
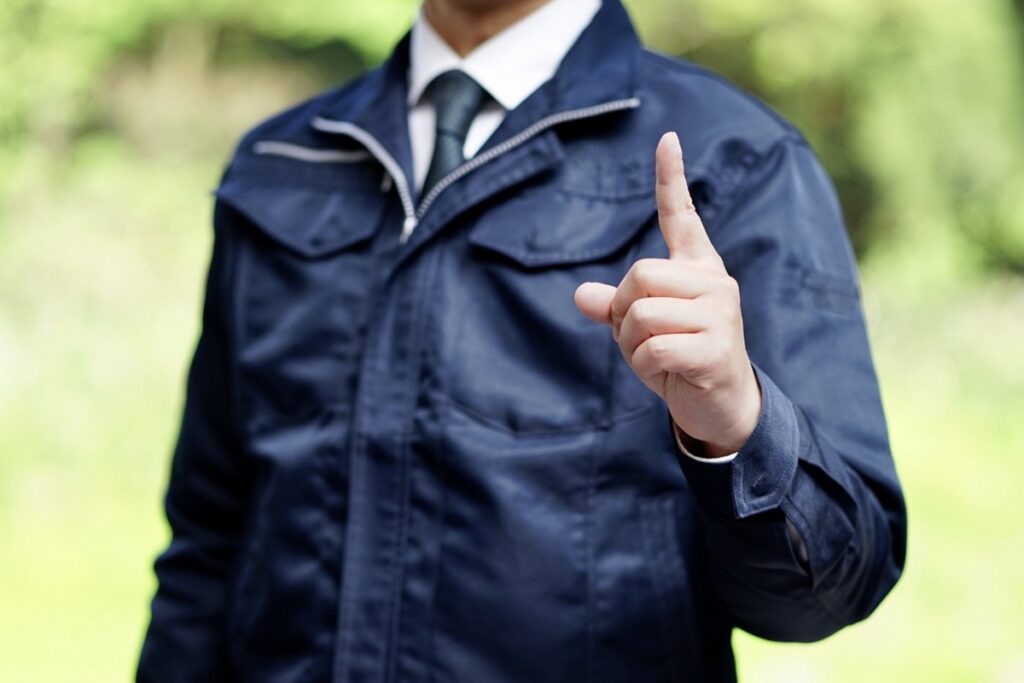
生産技術エンジニアには様々な役割があり、業務は多岐にわたります。
また、業界によって具体的な業務内容も異なります。
本記事では、切削加工における生産技術エンジニアの具体的な仕事内容として下記を紹介しています。
- 工程設計
- 工作機械の選定
- 治具の設計・製作
- ツーリングの選定
- 切削工具の選定
- 加工条件の設定
工程設計
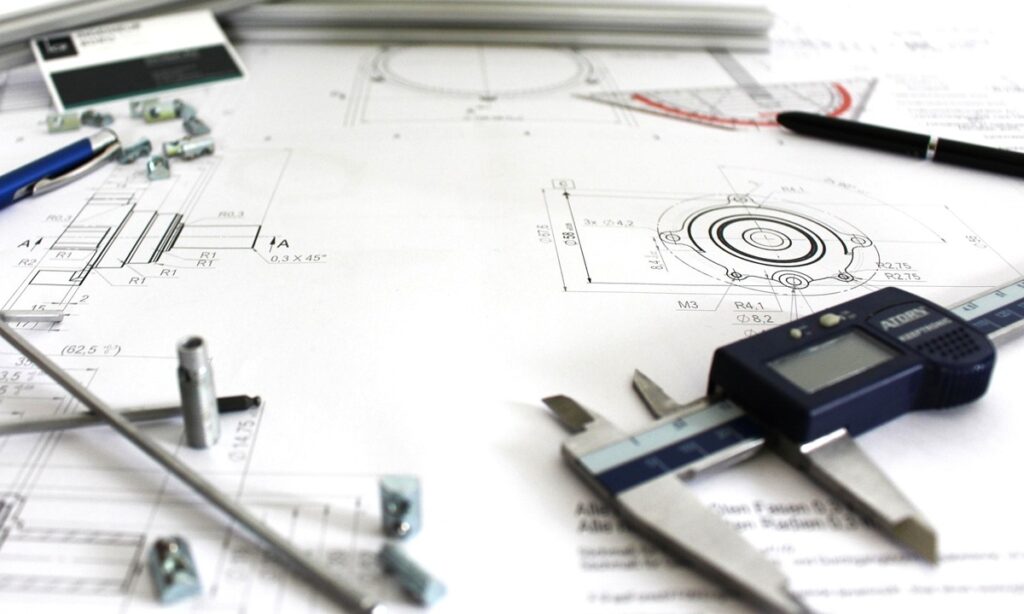
工程設計は「生産性」と「品質」のすべてを左右すると言っても過言ではない、極めて重要な業務です。
一方で、生産技術エンジニアとしての考えや想いを「コンセプト」として具現化できる場でもあり、その力量が問われる業務でもあります。
工程設計は、単に加工の順番を決めるだけの業務ではありません。
品質・生産性・現場負荷など、製造全体のバランスを俯瞰しながら組み上げていく、極めて高度な技術です。
だからこそ、生産技術エンジニアとしての経験や思考力が試されるやりがいのある仕事だといえるでしょう。
工程設計の出発点となるのは、基本的に「ワーク図面」のみです。
この図面をもとに、素材から完成品へと仕上げていく全体像を頭の中でイメージし、プロセスを組み立てていきます。
図面でまず確認すべき主なポイントは以下のとおりです。
- ワーク材質
- ワークサイズと重量
- 要求品質(幾何公差、データム、面粗度、百分台の寸法公差など)
- 取り代の有無と量
- クランプや加工基準にできそうな箇所
これらの情報をもとに、次のような事項を具体的に検討していきます。
- 粗加工・仕上げ加工の各工程とその順番
- 加工姿勢(加工時のワークの向き)
- 加工基準およびクランプ箇所の設定
- 使用する切削工具(形状、材質)およびツーリングの選定
- 加工条件(送り速度、回転数など)
- 想定される加工時間
- バリや切粉の発生に対する処置
工程設計において重要なポイントを紹介します。
要求品質を確実に担保できる工程
工程設計の第一の目的は、求められる品質を安定的に確保することです。
そのためには、加工基準と要求品質との整合性が取れているか、精度を実現できるような順番・ツーリング・切削条件になっているかを慎重に検討する必要があります。
また、それぞれの加工で「どの要素によって精度を保証しているか」を明確にすることも重要です。
たとえば、治具の精度、設備の性能、工具の精度など、何かしらの「拠り所」がなければ、万が一トラブルが発生した際の原因究明が難しくなります。
部品の使用用途・機能に適正な品質
加工対象の部品がどのような製品に使われるのか、どの部位がどのような機能を果たすのかを理解することも非常に大切です。
要求精度が過剰品質になっている場合も少なくありません。
機能に見合った適正な品質に落とし込むことで、加工はより効率的になり、生産性の向上にもつながります。
この点は、ぜひ設計者との対話・ディスカッションの中で擦り合わせていくことをおすすめします。
余談ですが、中小企業の現場でお話を伺うと、製品が「何に使われているのか分からない」と答える方が意外と多く見受けられます。
自分の携わっている部品が社会の中でどのような役割を果たしているのかを知ることで、「誇り」を持って仕事に取り組めるようになります。
そのような誇りは、ものづくりの楽しさにもつながり、将来的に製造業を志す若者を増やすきっかけにもなるかもしれません。
自分の関わっている製品に少しでも興味を持っていただければと思います。
生産計画数量に対して適正な加工時間
納期を守るためには、生産計画と加工時間の整合性をしっかり取る必要があります。
まずは加工時間を試算し、要求される生産数量を達成できるかを確認しましょう。
必要に応じて、以下のような工夫が求められる場面もあります。
- 工程を複数の設備に分散させる
- 特殊工具を使用して工程集約・時間短縮を図る
- 粗加工のみを外注する
ただし、無理な切削条件を設定すると、工具寿命が著しく短くなり交換頻度が増える、あるいは加工トラブルのリスクが高まるなど、生産性の低下を招く要因になります。
計画的な工程設計と、無理のない加工条件の設定が鍵となります。
工作機械の選定
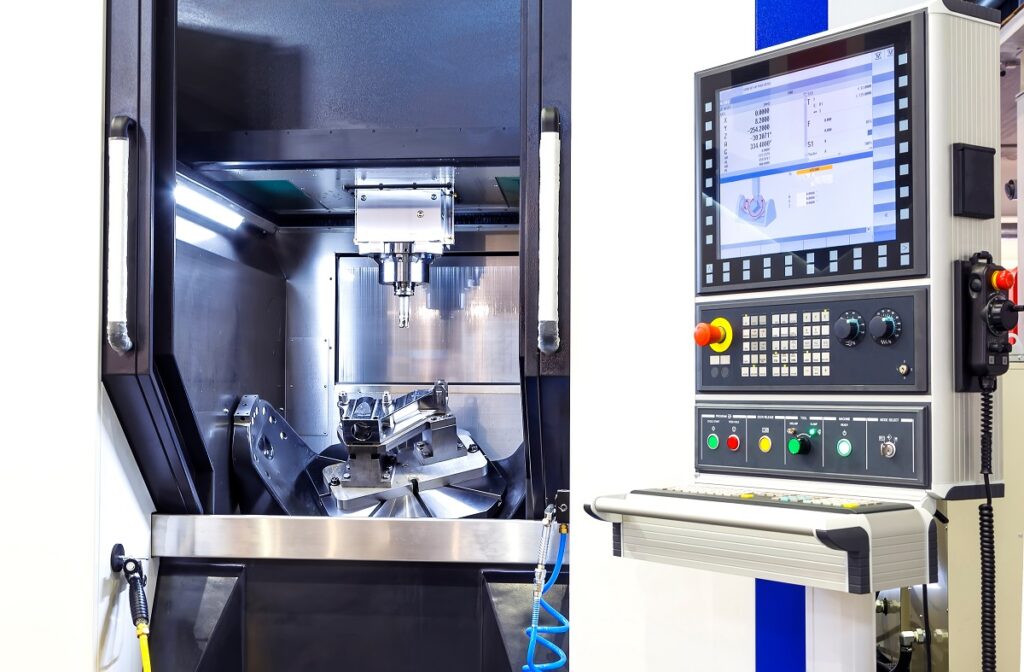
工作機械の選定は設備投資としての費用対効果はもちろん、長期的な運用効率や保守性にも直結する非常に重要な業務です。
工作機械の選定は、「今」だけでなく「これから」の生産活動にも影響する中長期的な投資判断です。
操作性、保守性、性能、将来の工程展開など、複数の観点から総合的に判断していくことが重要です。
工作機械の選定において重要なポイントを紹介します。
機械剛性と性能のバランス
工作機械の性能はワークの材質や加工取り代、要求される精度、加工工程の数に応じて必要な仕様が大きく異なります。
以下のような点を事前に整理しておくことで、適正なスペックの設備を選定できます。
- 切削に必要な主軸出力・トルク
- 駆動系の制御精度
- 熱変位補正の有無と性能
- ツールマガジン本数やATC機構の仕様
特に確認しておきたいのは、加工対象に対して主軸サイズやトルクが妥当かどうか、そして主軸まわり(コラム含む)の構造が必要な剛性を持っているかです。
なお、設備剛性についてはカタログスペックだけでは判断が難しいのが実情です。
実際の加工実績や他社ユーザーの使用感など、生の情報を基に検討することが現実的です。
工作機械メーカーからの情報だけでは限界があり、特にマイナス面は語られにくいため、客観的な視点で評価することをおすすめします。
既存設備との互換性
設備選定において最初に考慮すべきは、既存設備との互換性です。
複数の工作機械メーカーが混在している場合、操作手順が異なるため、現場作業者にとっては負担が大きくなります。
また、工作機械メーカーごとに保守部品を個別に在庫する必要があり、部品管理が煩雑になり効率も低下します。
可能であれば工作機械メーカーを統一することで、作業者の教育も簡素化され、保守部品の共通化やメーカー在庫の活用がしやすくなります。
特に自動ラインなどでI/O信号の接続仕様が絡む場合、統一された仕様によって設備間の連携がスムーズに行えるようになります。
保守サービス体制
突発トラブル時の保守対応スピードは、生産ロスを最小限に抑えるための重要な要素です。
選定の際には、以下のような保守体制を確認しておくと良いでしょう。
- 近隣にサービス拠点があるか
- 技術員の人数や対応可能な年齢層
- 対応時間(夜間・休日含む)
- 保守部品の在庫状況や入手性
主軸などの主要ユニットを工場で予備保管しておくことで、ユーザー側のダウンタイムを抑える取り組みをしている工作機械メーカーもあります。
こうした取り組みを参考にすることで、自社がどの程度の保守部品を在庫すべきかの判断材料にもなります。
治具の設計・製作
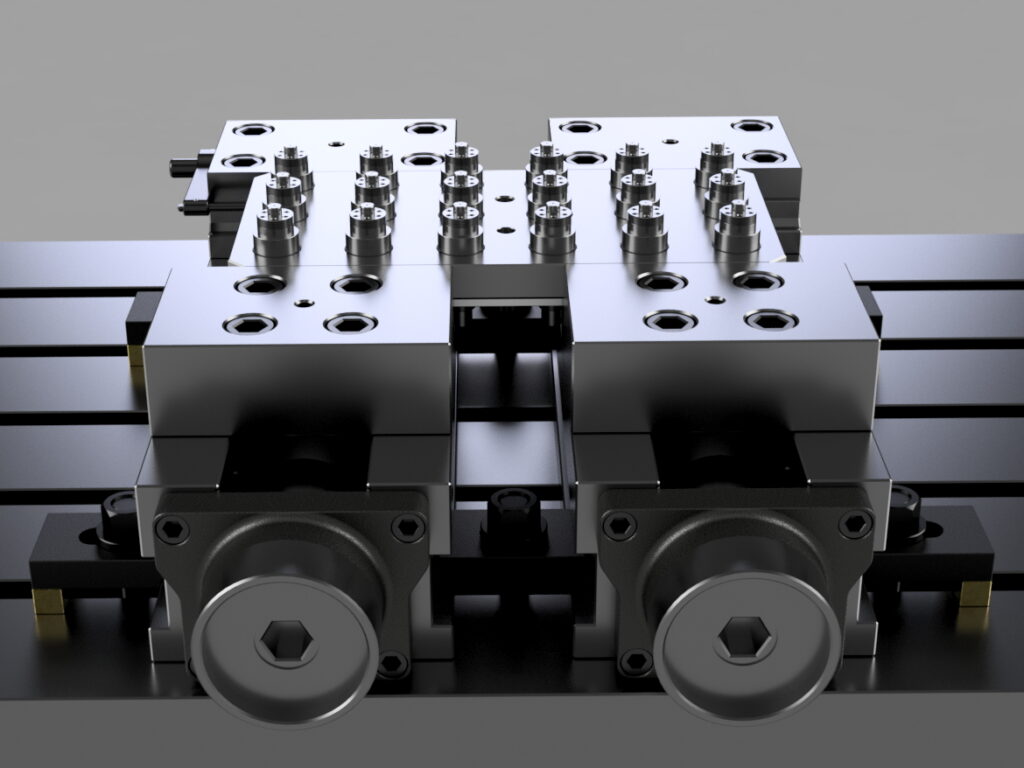
治具の設計・製作は切削加工における品質と生産性を大きく左右する重要な工程です。
治具の完成度は、設計者の実績や経験値に左右されます。
現時点では、治具設計における高度なシミュレーション技術はまだ十分に確立されておらず、現場で培われた知見が極めて重要な役割を果たしています。
治具設計においては、「加工精度」「作業性」「保守性」という三つの要素を高いレベルでバランスさせることが求められます。
実績と経験に裏打ちされた設計判断こそが、現場の品質と効率を大きく左右します。
治具の設計・製作において重要なポイントを紹介します。
加工負荷に対する受け構造の有無
設計の基本は、加工中に発生する切削負荷に対して確実に受けが設けられていることです。
負荷を適切に受け止められない治具では、精度不良や振動の原因となり、品質を安定させることができません。
段取り性と再現性
段取りのしやすさを考慮した構造も、作業効率や再現性を高めるために欠かせない要素です。
誰が扱っても同じようにワークがセットできる構造であれば、作業時間の短縮だけでなく、加工品質の安定化にもつながります。
クランプ構造と加工歪み
クランプの影響にも細心の注意が必要です。
製品精度を安定させるうえでの重要なチェックポイントが下記です。
- 加工中の歪みに対して、クランプが不要な応力を加えていないか
- クランプの解除時に残留応力が発生し、仕上げ寸法に影響を与えないか
場合によっては、加工中にクランプ圧力を変えて加工精度を確保する処置をする場合もあります。
ビビり対策
加工中のビビり(振動)に強い構造かどうかも、加工品質に直結します。
特にビビりやすい箇所にはナチュラルサポートを設置できる設計にすることで、振動抑制効果が得られ、より安定した加工が可能になります。
切削工具のアプローチ性
切削工具が最短経路でワークにアプローチできる形状であるかも重要なポイントです。
アプローチ性が良ければ、無理な工具動作を避けたり、工具剛性の確保ができるため、工具寿命の改善や加工時間の短縮といった生産性向上にも寄与します。
交換部品の最小化と保守性
治具の構成部品である加工基準ピンやクランパーなどは、最小限の範囲で交換できる仕様が理想です。
これにより、保守作業の工数を抑えつつ、治具全体の再現性や信頼性を維持することができます。
ツーリングの選定
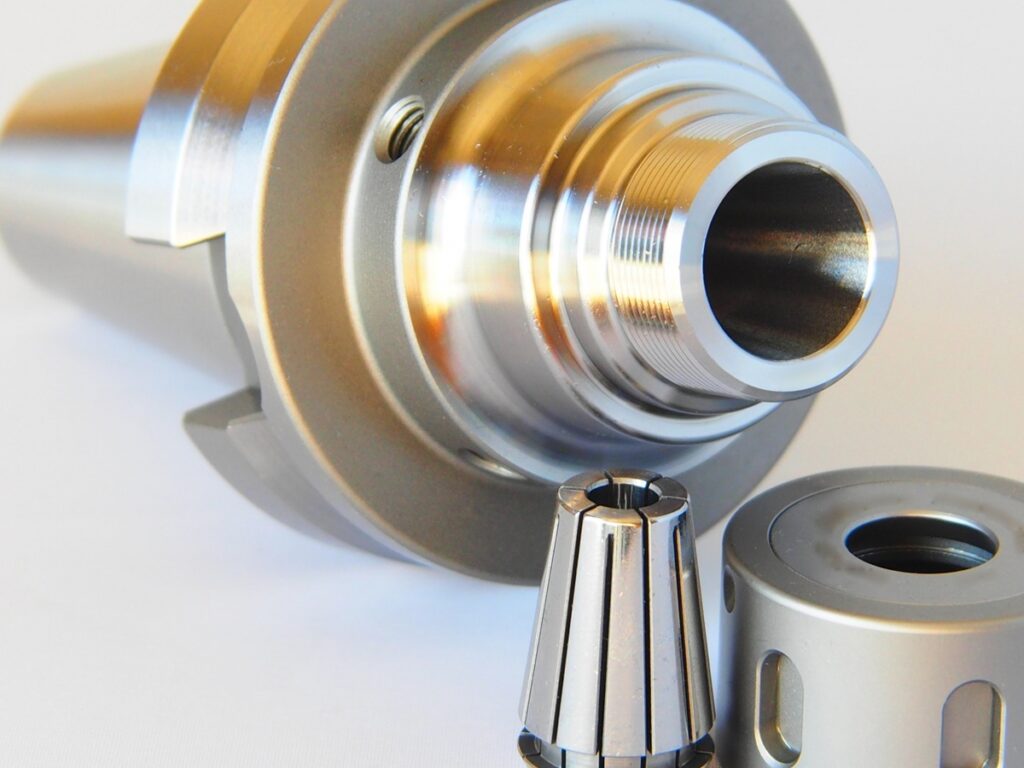
ツーリングの選定は切削加工における加工精度・工具寿命・作業性に大きく影響します。
適切なツーリングの選定によって工具性能を最大限に引き出し、加工の安定性・品質・生産性を向上させます。
工具だけでなく、ツーリングとの「組み合わせ」まで含めたトータルな視点で検討を進めましょう。
ツーリングの選定において重要なポイントを紹介します。
切削負荷・剛性に基づく選定
切削方向や切削負荷に応じて、十分な工具保持力と剛性を持ったツーリングを選ぶことが重要です。
特に高負荷切削や深切込み加工においては、ツールホルダーの剛性不足によるビビリや振動、たわみが加工品質に影響を与えます。
そのため、チャッキング部の構造、ゲージライン長、メーカーの切削加工データなどの確認が必要です。
要求品質に応じた精度の確保
高い加工精度が求められる工程では、振れ精度が良好なツーリングが不可欠です。
ツールホルダーの振れが大きいと、寸法精度や表面粗さに悪影響が出るだけでなく、工具寿命の低下にもつながります。
繰り返し使用時にも安定した振れ精度を保てるツールホルダーが理想的です。
動バランス性能
高速回転が必要な加工では、ツールホルダーの動バランス性能が重要です。
バランスが悪いと高速回転時に振れ精度が悪化し、加工不良や工具破損のリスクが高まります。
対応する回転数に対して、バランス等級が適合しているかを事前に確認しておくことが必要です。
クーラント供給方式
ツーリングを選定する際には、クーラントの供給方式にも注意が必要です。
センタースルーやサイドスルーなど、加工点にしっかりクーラントが届く構造になっているか確認しましょう。
特に深穴や高速加工では、切削点の冷却・切りくず排出が安定加工に直結します。
ツールホルダー種別
ツールホルダーには様々な種類があり、それぞれ特性が異なります。
使用用途や品質要求に応じて、最適なチャッキング方式を選定することが重要です。
汎用性、把握力、振れ精度、剛性、作業性を考慮して、選定しています。
コレットチャック仕様
コレットチャック1つをとっても、メーカーごとに仕様が異なります。
テーパー角度、コレットの把握方式で各種メーカーに特徴があり、同じサイズでも把握力や振れ精度に差が出るため、要求品質に合わせて選定する必要があります。
既存設備・ラインナップとの整合性
工場内の既存ツーリングとの互換性も重要なポイントです。
下記のポイントを確認し、無駄な種類の増加を避けることで管理コストを抑えられます。
- 共通ツールホルダーの使用による在庫の共通化
- 予備品の有無・整備状況
工具長の最適化
工具が治具やワークに干渉しない限り、できるだけ短いツーリングを選定することで、剛性を高めてビビリのリスクを減らせます。
また、工具が長くなるほどたわみの影響も大きくなるため、必要最小限の突出し量に抑えるのが基本です。
切削工具の選定
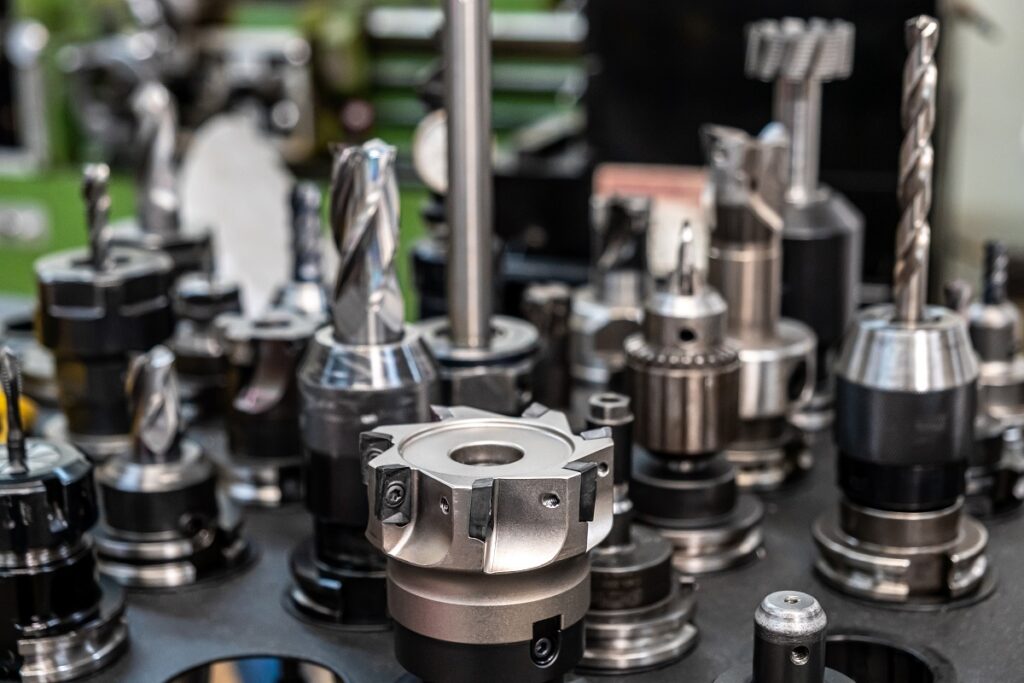
切削工具の選定は、加工品質・加工時間・コストに直結する非常に重要な業務です。
正しい工具を選定することで、安定した加工と高い生産性を実現できます。
切削工具の選定は「加工技術」と「経済性」の両面から検討する総合判断業務です。
現場の声や過去の実績、商社やメーカーからの最新情報を活用しながら、最適な選定を行うことが求められます。
切削工具の選定において重要なポイントを紹介します。
目標加工時間と工具寿命のバランス
工程設計で設定した目標加工時間を達成できる工具を選定します。
高速加工によってサイクルタイムを短縮する一方で、工具寿命とのバランスも重要です。
過剰な高速加工による寿命低下は、生産性を下げるリスクがあるため、最適な条件で最大効果を出せる工具の選定を心がけます。
高精度が要求される工程への対応
品質要求が厳しい工程では、粗工程から精度を意識した工具選定が必要です。
例えば、5D以上の深穴リーマ加工では、仕上げリーマの性能を最大限発揮させるために、下穴加工用のドリルやエンドミルも、真直性・真円度・円筒度が高いものを選定する必要があります。
全体の工程で精度が保証される構成を意識します。
工具の材質・コーティング
工具の材質やコーティングも重要です。
ワーク材質や加工条件に応じて、耐摩耗性・耐熱性・切れ味・溶着防止性能などが最適化されているコーティングを選定します。
要求品質を安定してクリアできる仕様であるかを事前に確認しておくことが不可欠です。
工具費の抑制
工具費の抑制も重要な視点です。
下記のポイントを意識し、導入・運用コストの最適化を目指します。
- 多コーナー仕様で1本あたりの使用回数を増やす
- 再研磨可能な工具を選ぶ
- 既存工程で流用できる工具がないかを確認する
工具トラブルへの柔軟な対応力
加工中にトラブルが発生した場合に備えて、工具ラインナップの柔軟性も考慮します。
形状やコーティングのバリエーションが多い工具は、トラブル時の代替案を立てやすく、現場対応力が高まります。
工具の供給安定性・入手性
量産時においては、工具の供給安定性・入手性が非常に重要です。
下記のポイントなどを優先的に検討します。
- 在庫リスクが少ない標準品
- 商社やメーカーから迅速に入手できる体制
また、型式変更による廃番リスクもあるため、可能な限り最新モデルやラインナップが豊富な工具を選ぶことが望ましいです。
工具在庫の取り扱いリスク
新しい切削工具を導入することによって、従来使っていた工具が不要になる場合は、在庫処分や棚卸資産のロスリスクも考慮する必要があります。
特に高額な特殊工具は、事前に在庫量や用途の洗い出しをしておくと、無駄なコストを抑えることができます。
加工条件の設定
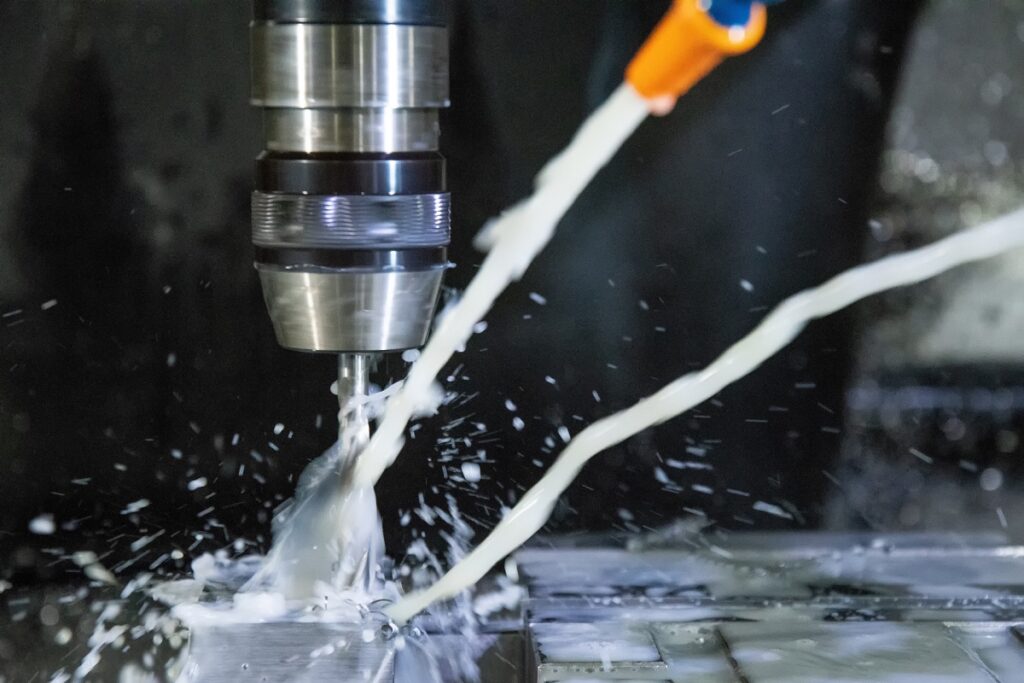
加工条件の設定は、品質・生産性・工具寿命のすべてに影響を及ぼす重要な業務です。
適切な条件設定により、安定した加工と高いコストパフォーマンスの両立が可能になります。
加工条件の設定は、「理論」と「実践」、そして「経験」の融合で成り立ちます。
安定した加工と効率的な生産を両立させるために、状況に応じた柔軟な条件設定を心がけることが重要です。
加工条件の設定において重要なポイントを紹介します。
加工条件の妥当性
現在設定している加工条件が、工具メーカーのカタログ推奨値と比較してどの位置にあるのかを確認します。
特に注目すべきは、使用済み工具の摩耗状態です。
設定した寿命に対して摩耗に余裕があるようであれば、条件の強化(切削速度・送り速度の向上)を検討できます。
逆に摩耗が過大であれば、条件を見直す必要があります。
カタログ値を基準に初期加工条件を設定
加工条件の初期設定では、まずは安全を見越してカタログの標準中間値に合わせた条件とするのが基本です。
特に新規品番や新素材など、過去実績のない条件では慎重な立ち上げが重要です。
安定品質が確認できれば、生産状況に合わせて切削条件を調整していきます。
安定加工を優先した条件設定
最も重要なのは安定して品質が確保できる加工条件であることです。
いくら加工時間が短縮できても、加工精度や工具寿命が不安定では意味がありません。
経験値と外部情報の活用
過去の社内実績やノウハウがある場合は積極的に参照します。
また、切削工具メーカーや機械工具販売店からの技術情報も非常に有益です。
工具材種や被削材の組み合わせに応じた実績ベースの加工条件を提案してもらうことで、より信頼性の高い条件設定が可能になります。
サイクルタイムの短縮
算出された加工時間が生産計画に対して不足している場合は、粗加工工程から条件を見直し、サイクルタイム短縮を図ります。
この際、切削速度(周速)を上げすぎると、工具寿命に大きな影響を与えるため注意が必要です。
できる限り高送り化(切込みや送り速度の最適化)によって効率化を図る方が、寿命とのバランスが取りやすくなります。
表面粗さと理論値の乖離
要求される表面粗さに対し、理論面粗さと実測値にどれだけ乖離があるかを確認します。
工具の切れ味や振動、機械剛性などの影響も加味して、狙いの表面粗さを実現できる条件に調整していきます。
五感を活かした総合的な判断
加工音・切粉の状態・ワークの仕上がり・工具の損傷具合など、現場で得られる五感の情報を総合的に判断して最適な条件に仕上げていきます。
これこそが現場の生産技術者の真価が問われる場面です。
辰星メタルパートナーの紹介
今回記事を執筆いただいた辰星メタルパートナーを紹介します。
辰星メタルパートナーは切削加工専門の生産技術エンジニアが提供する「生産技術アウトソーシングサービス」を提供しています。
ミッション:豊かで愉しい「ものづくり業界」を創る
先人の方たちが築いてくれた誇り高い業界に感謝して、生産技術エンジニアとして未来にバトンを繋ぎます。
未来のエンジニアが愉しく働ける環境を創り、日本そして世界の製造業の発展に貢献します。
コンセプト
雇用から業務委託にすることで、「生産技術エンジニアの雇用コスト半分以下を実現」し、人財不足による改善停滞、競争力低下の課題を解消します。
メインサービス:生産工程の改善支援
大手製造業含む30社以上の改善実績経験がある専門エンジニアが、三現主義による現状分析をもとに、最適な改善アクションプランを提示し、伴走型の改善サービスを提供します。
改善実績:
〇油圧系部品生産性向上
⇒NCプログラム解析し、加工パス、条件見直し、工具改善により20%改善
〇燃料ポンプケース生産性向上
⇒NCプログラムの解析、加工条件見直しにより30%改善
〇スプール穴旋盤リーマ穴加工、突発不良改善
⇒加工工程最適化(加工工具見直し、工程変更)により、突発不良件数ゼロ
その他サービス:工程設計支援、新規設備導入支援、専門技術支援、専門技術教育
編集長コメント
「切削加工における生産技術エンジニアの具体的な仕事内容」いかがでしたか。
実際に切削加工の現場で生産技術をされている方の情報を知ることができる機会は少ないと思いますので、こちらの記事を参考にしていただければと思います。
関連記事
ライター・執筆者情報
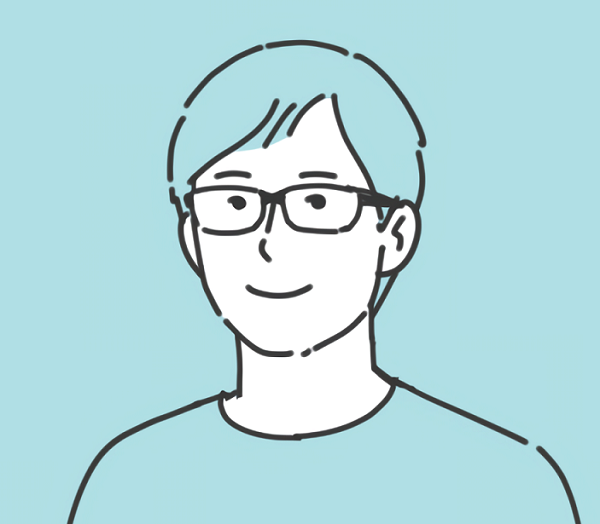
本記事は生産技術アウトソーシングサービスを提供する辰星メタルパートナーの松田様に執筆いただき、タクミセンパイの服部が編集しました。
私は工具メーカーでの営業とマーケティングの経験を活かし、切削工具と切削加工業界に特化した専門サイト「タクミセンパイ」を2020年から運営しています。
私(服部)の実績や経歴については「運営について」に記載しています。
タクミセンパイとして収集した最新情報をもとに、ここでしか読めない独自視点の記事や調査データを提供しています。
中立的な立場として発信する情報は、読者から「信頼できる」と高い評価を得ています。
メールマガジンのご案内
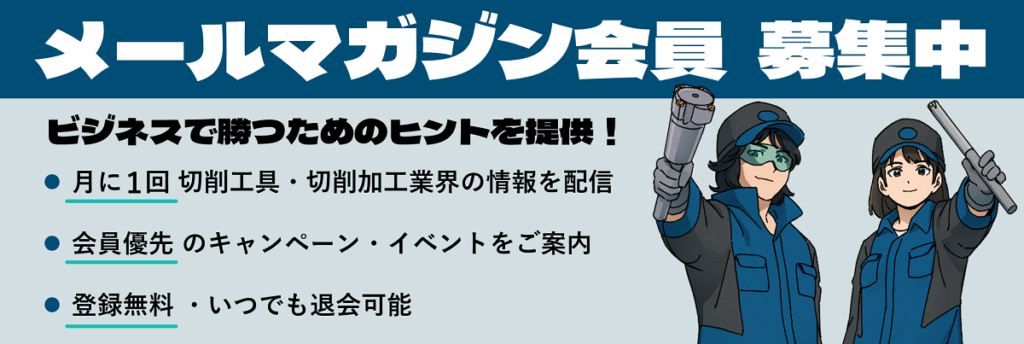
タクミセンパイでは月に1回メールマガジンを配信しております。
お届けする内容としては下記になります。
・切削工具・切削加工業界の新着オリジナル記事
・切削工具・切削加工業界のオススメ記事
・イベント情報
・会員優先のキャンペーン・イベント情報
ご興味のある方は「メールマガジンのご案内」ページをご確認ください。
会員登録は無料でいつでも退会可能です。