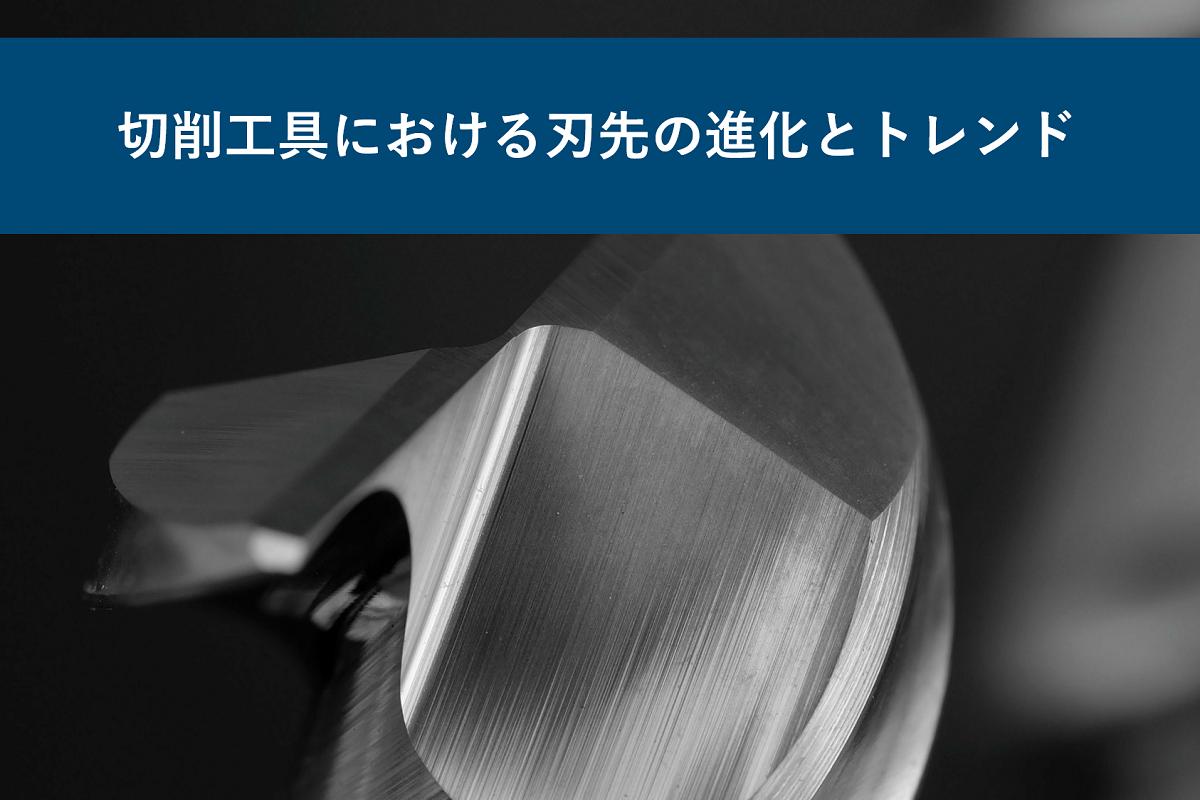
切削工具における刃先の進化とトレンドを知りたくありませんか。
この記事は切削工具の製造に精通したライター「すなおさん」に記事執筆を依頼し、切削工具と切削加工業界に特化した専門サイト「タクミセンパイ」が編集しました。
本記事では切削工具材種別の刃先の進化、切削工具製造技術による刃先の進化、切削工具の刃先トレンドについてまとめています。
この記事を読むことで、切削工具の刃先に関する理解を深め、加工形態や被削材に対して最適な工具を選定できるようになります。

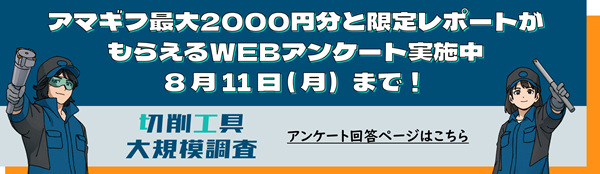
切削工具における刃先の進化とトレンド
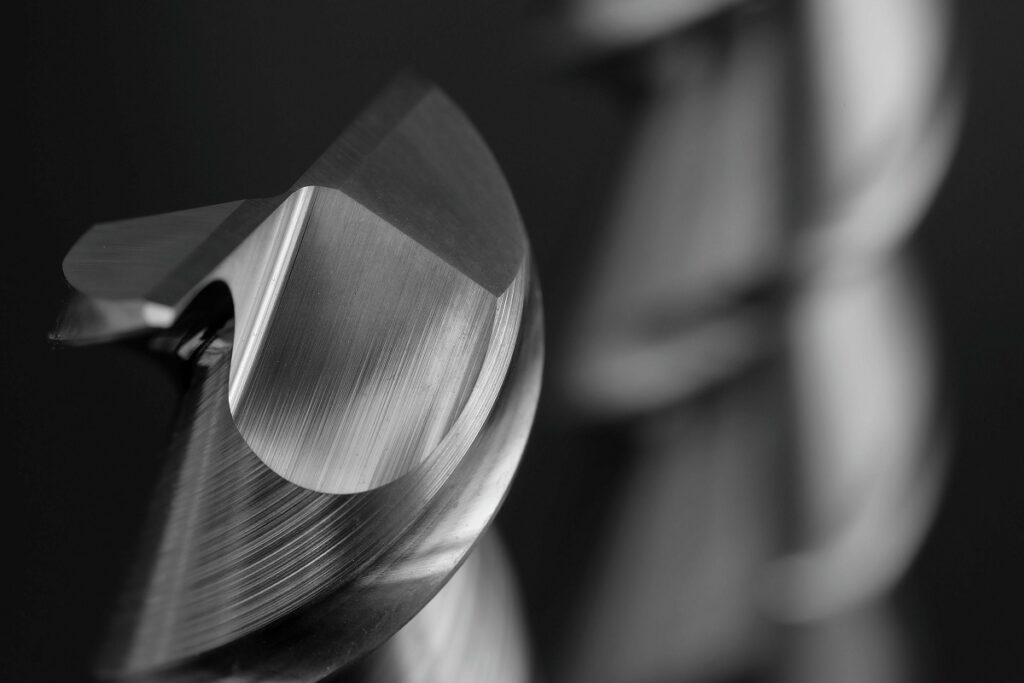
切削工具が実際に加工をしている部分は刃先です。
切削工具の刃先に関する理解を深めることで、加工形態や被削材に対して最適な工具を選定できます。
刃先への理解を深めるためには、まず用語を理解しなければなりません。
以下に一般的な刃先用語と働きを紹介します。
頂角
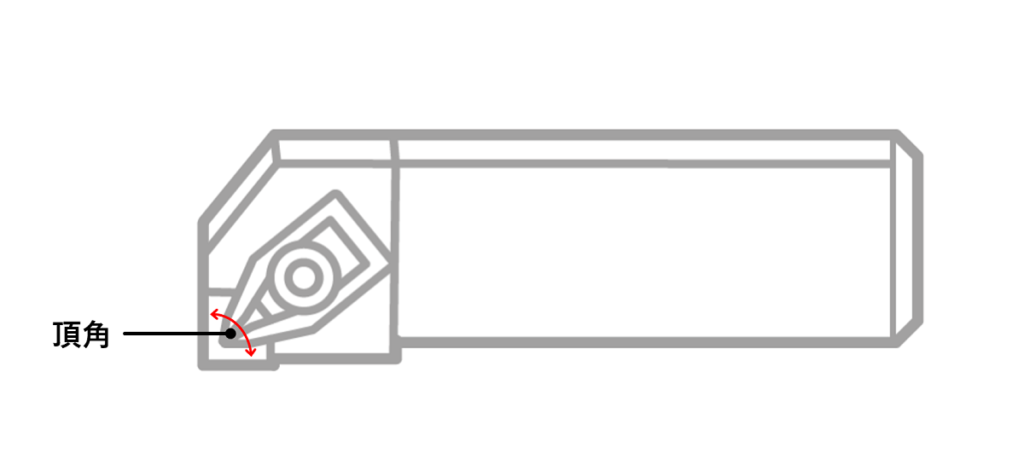
バイトやインサート工具において、工具上面から見た刃先の先端角度が頂角です。
頂角が小さいほど切削抵抗が低くなり、剛性が低くなります。
反対に頂角が大きいほど剛性が高くなり、切削抵抗が高くなります。
刃物角
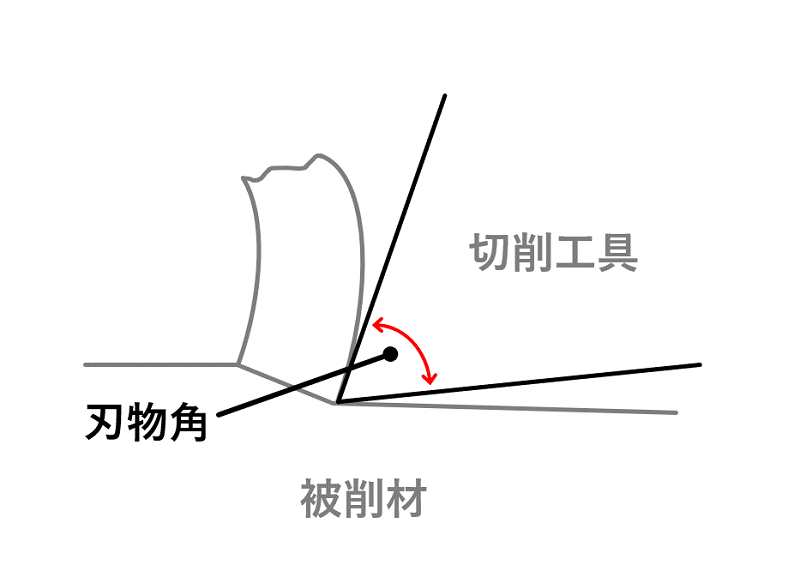
切削工具が被削材に食い込む際の刃先の角度が刃物角です。
刃物角を小さくすると切れ味が上がって切削抵抗が下がりますが、一方で刃先強度が下がって欠損やチッピングが発生しやすくなります。
すくい角

切削工具が被削材を削る際に、進行方向前面に切くずが発生します。
切削工具は切くずをすくい上げるように動き、切くずを流している面をすくい面と呼びます。
被削面からみた垂直面とすくい面のなす角がすくい角です。
垂直面から進行方向と逆に角度がついている場合はすくい角が正、進行方向側に角度がついている場合はすくい角が負になります。
すくい角を大きくとると切れ味が上がって切削抵抗が下がりますが、一方で刃先強度が下がって欠損やチッピングが発生しやすくなります。
逃げ角
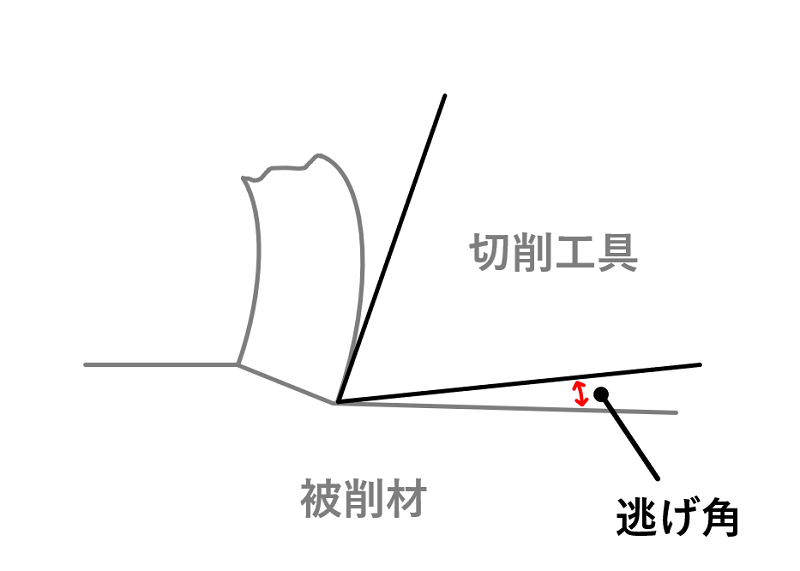
切削工具と被削材が干渉しないように逃げをつくる角度です。
被削面とのなす角度を逃げ角と言います。
基本的には逃げ角は干渉さえ避ければ、大きくとる必要はありません。
しかし、逃げ角を大きくとるとビビリにくくなることや、逃げ面摩耗幅が小さくなるメリットがあります。
ホーニング
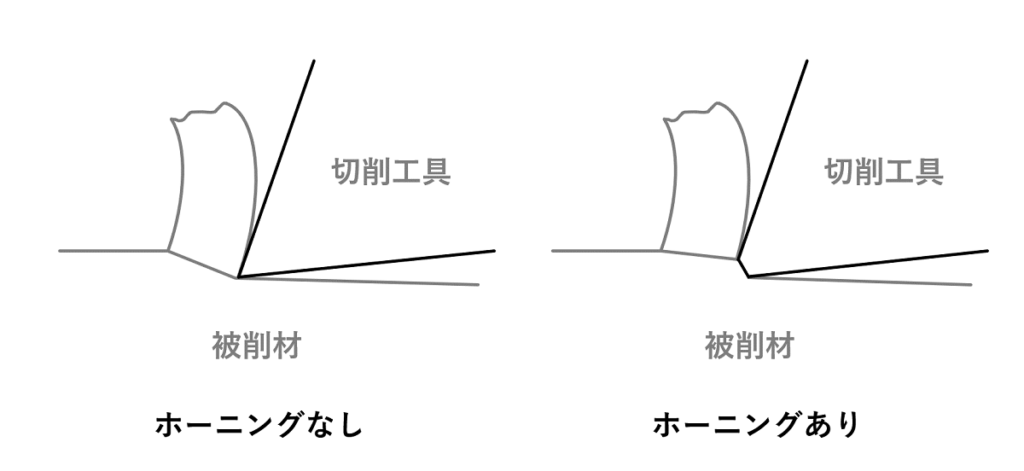
ホーニングとは切削工具の刃先強度を上げるために行う刃先処理です。
切削工具にホーニングを施すことで刃先強度が上がりますが、切削抵抗が増えます。
大きく分類して刃先を丸くする丸ホーニングと、面取りを施すチャンファーホーニングがあります。
丸ホーニングとチャンファーホーニングを比較すると、より刃先強度に優れているのが丸ホーニング、切れ味に優れているのがチャンファーホーニングです。
工具材種、被削材によっては両方のホーニングを施すことがあります。
チップブレーカー
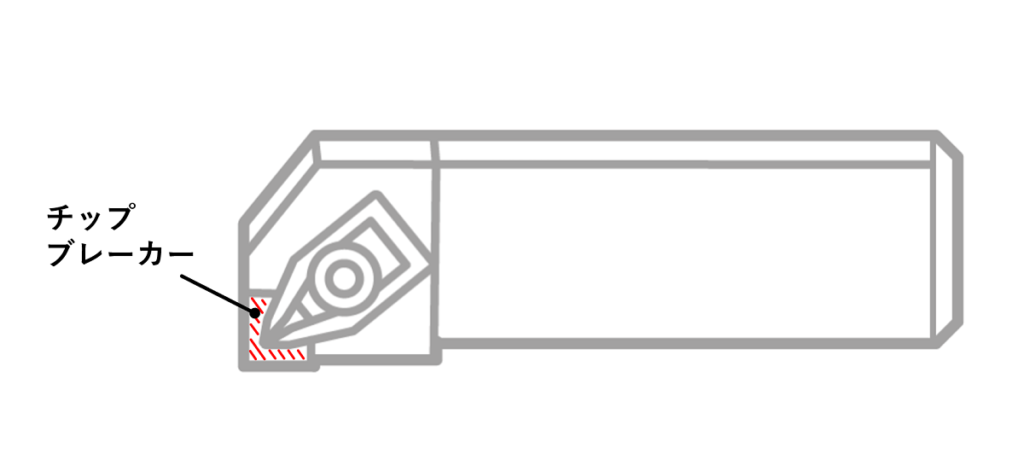
インサート工具において、切くずを処理するために「すくい面」に設けられている溝や障壁のことを指します。
旋削加工において切くずが長く伸びると、切りくずが切削工具や被削材に絡まって、工具寿命の低下や被削材に傷が入るデメリットがあります。
長く伸びた切くずは作業者に接触することもあり危険です。
切くずが長く伸びないように、チップブレーカーによって切くずの流れをコントロールし、短いうちに千切れるように設計されます。
切削工具材種別の刃先の進化
ハイス切削工具
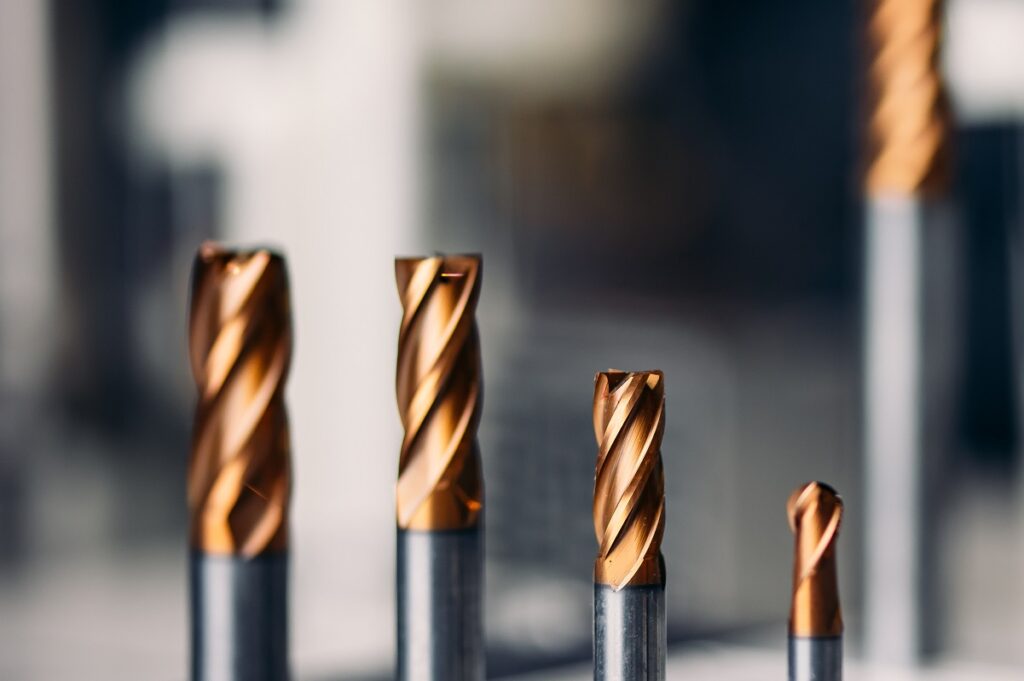
ハイスが切削工具に使用されるようになった頃は、熱処理後の高硬度鋼材は加工できませんでした。
ハイス切削工具で熱処理前の鉄鋼材料を加工する際は、ホーニングなしで切れ味を重視します。
切削工具の中でハイスは靭性が高く、チッピングや欠損に強い材種です。
刃先への熱の集中による硬度低下をさけるため、切れ味を重視してホーニングを施すことは少ないです。
超硬合金切削工具
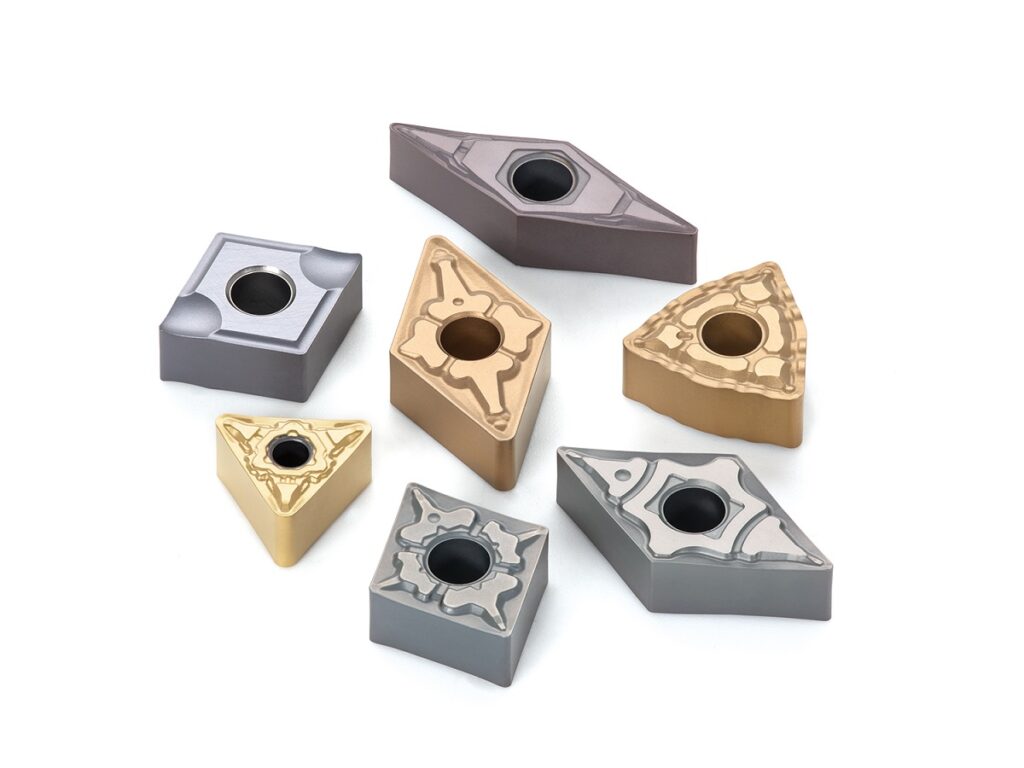
超硬合金の登場により、熱処理後の高硬度材料でも切削加工ができるようになりました。
高硬度材料の加工において、チッピングや欠損が1番の問題です。
対策としてホーニングを施すことが多くなります。
加工形態に合わせて、丸ホーニングかチャンファーホーニングを選択しますが、両方を施す場合もあります。
旋削加工では切くず処理のためにチップブレーカーが重要です。
CBN切削工具
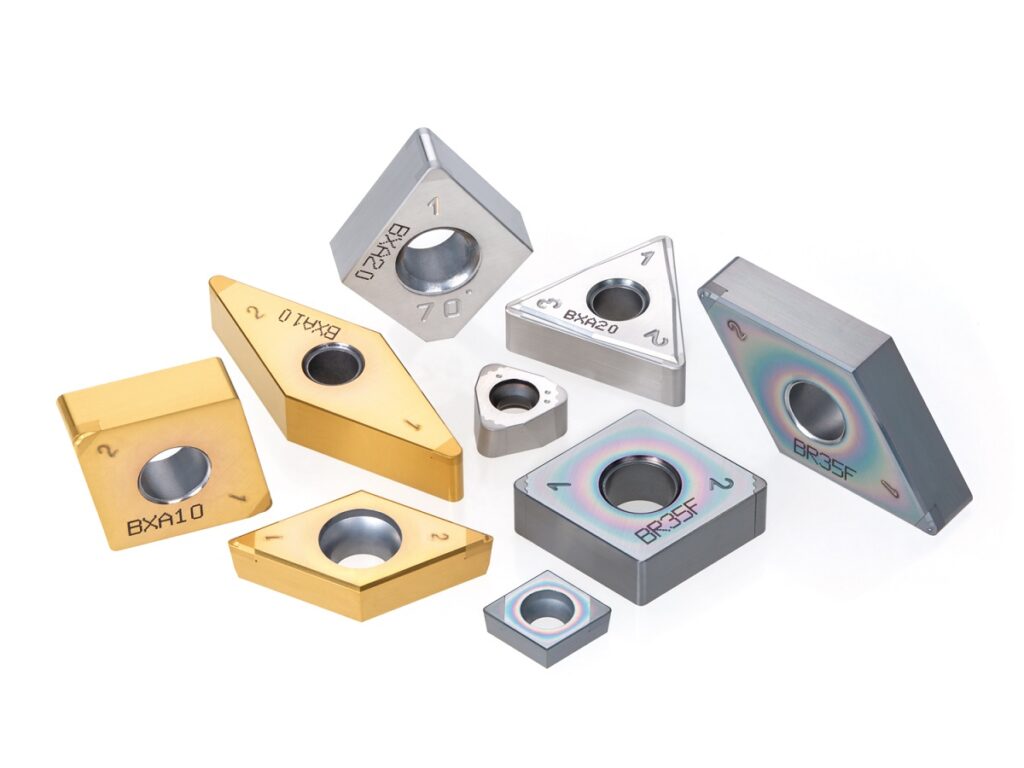
CBNは主に高硬度材料を加工する用途で使用される工具材種です。
工具材種が高硬度材料より硬く脆いため、刃先には必ずと言っていいほどホーニングが施されています。
微細な仕上げ加工や鋳鉄の加工では、ホーニングを施さない場合もあります。
CBN切削工具で高硬度材料の仕上げ加工を行う場合は、切れ味を重視してチャンファーホーニングを施すことが多いです。
丸ホーニングのみを施す場合は少なく、チャンファーホーニングと組み合わされることが多くなります。
PCD切削工具
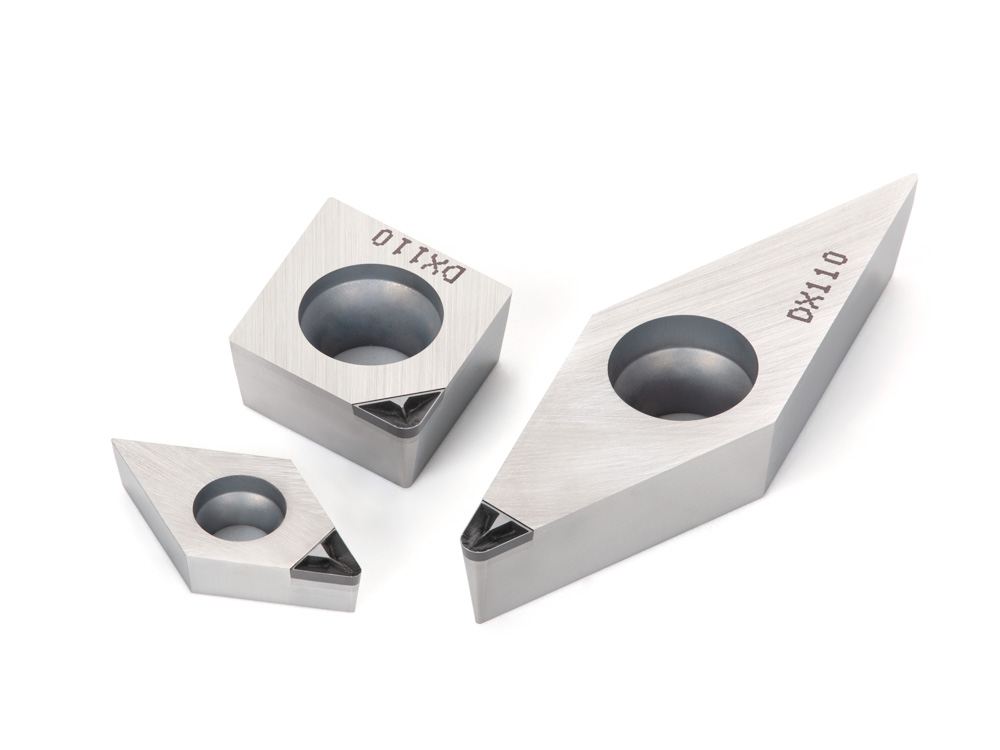
PCDは非鉄材料加工において長寿命を発揮する材種です。
アルミニウムや銅など鉄鋼材料より柔らかく、溶着しやすい材質を加工するため、すくい角を大きく取る場合が多くなります。
切れ味を重視するためにホーニングを施すことがほとんどありません。
超硬合金の加工に使用される場合は、刃先強度を上げるためにすくい角をなくし、ホーニングを施す場合もあります。
切削工具製造技術による刃先の進化
工具研削盤のNC制御やCAMの発達によって複雑で微細な加工が可能となり、CBN切削工具でも研磨によるチップブレーカーが施されるようになっています。
ホーニングの分野でも、チャンファーホーニングが丸ホーニング並みに小さく加工できるようになっています。
以前は研磨では再現不可能な複雑なチップブレーカー形状は、超硬工具の型押しで成型したものしか見られませんでした。
型彫りレーザー加工機の登場で、PCD切削工具やCBN切削工具にも複雑な形状のチップブレーカーを施せるようになり、加工面品位や加工効率の向上が図られています。
切削工具の刃先トレンド
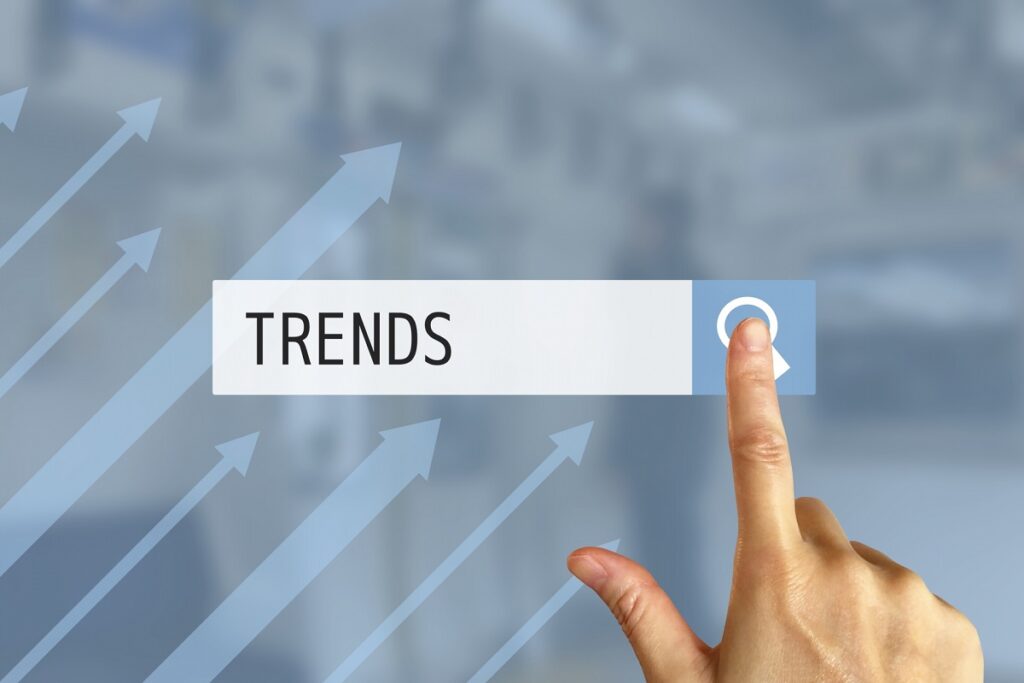
自動車の燃費性能に対する要求で、軽量化を目的としたアルミニウム合金部品の採用が多くなっています。
アルミニウム合金の加工にはPCD切削工具が多く使われており、溶着防止のため「すくい角」を大きくし、ホーニングなしで切れ味を向上させていることがほとんどです。
今では加工面品位の確保のため、型彫りレーザー加工機による複雑な形状のチップブレーカーを採用することも少なくありません。
ハイブリットカー部品には銅とアルミニウム合金、銅と鋼などの積層材料が多く使われています。
積層材料に鋼が使用されている場合には、PCD切削工具にホーニングを施してチッピングや欠損の対策をすることが増えてきています。
高硬度焼入鋼の研磨加工を、CBN切削工具での切削加工に置き換えることが増えてきました。
加工面品位を確保するために切くずの処理が重要となり、刃先で大きな役目を担うのがチップブレーカーです。
工具研削盤のNC制御技術の向上で、障壁型のブレーカーを採用しているCBN切削工具も少なくありません。
刃先部分のみ1段下げて加工することで、切くずをカールさせる壁を作ります。
溝や型彫りと異なり、対欠損性を確保したまま切くず処理を向上させています。
高硬度材料を加工するCBN切削工具に最適です。
研磨加工を切削加工に置き換える動きは超硬金型の分野でも活発になっています。
超硬金型を切削加工で鏡面仕上げするバインダレスPCD切削工具なども登場しています。
チッピングや欠損の対策と、切れ味の両立のためにチャンファーホーニングと丸ホーニングを組み合わせた刃先処理も増加傾向にあります。
関連記事
ライター・執筆者情報
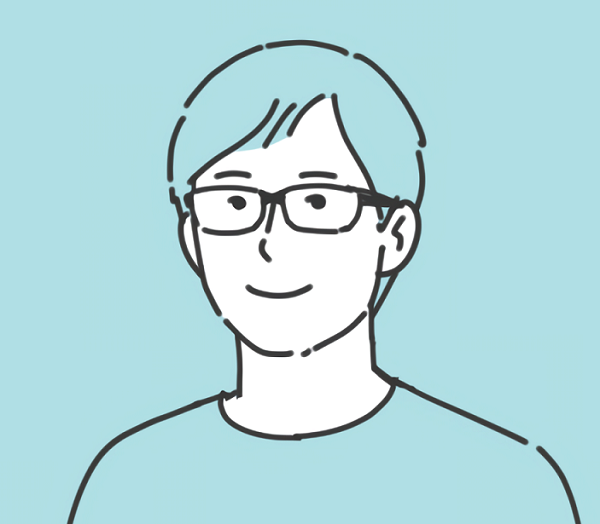
本記事は切削工具の製造に精通したライター「すなおさん」に執筆いただき、タクミセンパイの服部が編集しました。
私は工具メーカーでの営業とマーケティングの経験を活かし、切削工具と切削加工業界に特化した専門サイト「タクミセンパイ」を2020年から運営しています。
私(服部)の実績や経歴については「運営について」に記載しています。
タクミセンパイとして収集した最新情報をもとに、ここでしか読めない独自視点の記事や調査データを提供しています。
中立的な立場として発信する情報は、読者から「信頼できる」と高い評価を得ています。
メールマガジンのご案内
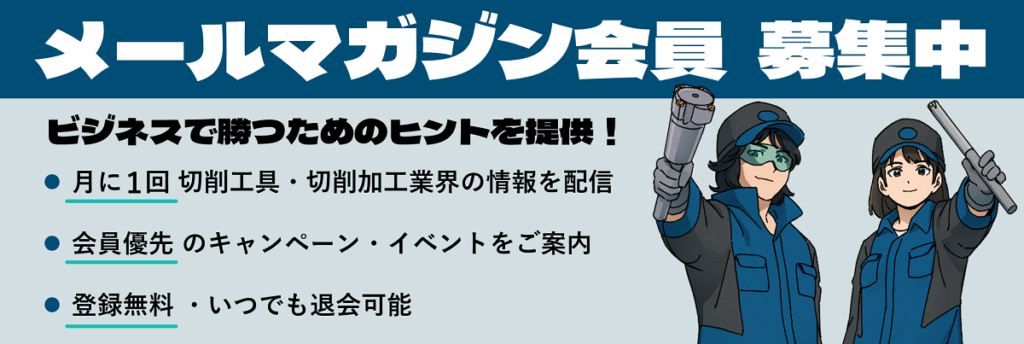
タクミセンパイでは月に1回メールマガジンを配信しております。
お届けする内容としては下記になります。
・切削工具・切削加工業界の新着オリジナル記事
・切削工具・切削加工業界のオススメ記事
・イベント情報
・会員優先のキャンペーン・イベント情報
ご興味のある方は「メールマガジンのご案内」ページをご確認ください。
会員登録は無料でいつでも退会可能です。